|
- Q: Why Ice Thermal Storage for Process Cooling Projects
- A: Because only ice can provide a system that yields:
|
? |
- 1. Reduced chiller size. Variable capacity that provides quicker pulldown and less compressor wear
|
- 2. Constant low temperature supply
|
- 3. Less connected kW and smaller electrical equipment
|
- 4. Reduced energy costs by providing flexibility in when energy is used
- 5. Reduced maintenance by using smaller equipment with flexibility in service schedules
|

- Reduced Chiller Size
|
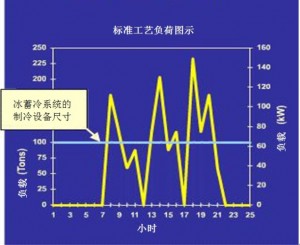 |
By designing a process cooling system with ice storage, the size of the chillers and cooling towers or air-cooled condensers required are significantly reduced. The chiller no longer needs to be sized for the peak load but now can be sized for the average load with the ice storage handling the peak cooling requirements. The savings that result from the use of smaller chillers and heat rejection equipment and less connected horsepower offset the cost of the ice thermal storage equipment. |
|
|
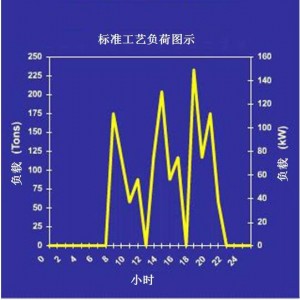 |
The ice thermal storage system will deliver most system load variations. The flow and entering water temperature set the instantaneous capacity. The ice thermal storage system will maintain a constant supply temperature regardless of the variations in instantaneous cooling demand.
|
|
|
Many processes have high pulldown loads at the start of the cooling requirement. Ice storage is an excellent solution to handling these loads quickly and without increasing chiller size. At the beginning of the pulldown period when the instantaneous load is high, the ice thermal storage system will compensate for the increased load since it has the cooling stored and ready to use and will attempt to deliver the full cooling requirement. By controlling the water flow and temperatures entering and leaving the ice thermal storage unit, the rate of cooling can be controlled. |
|
Since ice thermal storage systems are sized to operate primarily at full capacity, compressor wear from capacity adjustments (compressors cycling on and off) is minimized, providing maintenance savings over the life of the compressor. |

- Constant Low Temperature Supply
|
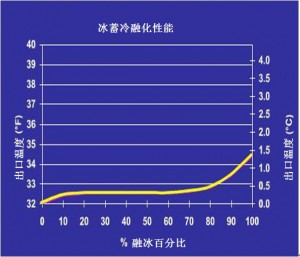 |
The ice thermal storage system can provide a constant 34°F (1°C) supply water to a process. The cold water can reduce the cooling time for many processes and allow increased production. |
|

- Less Connected kW
|
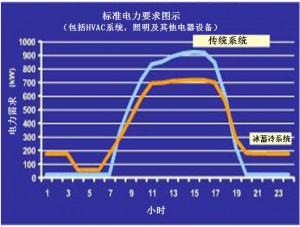 |
Since the compressor in an ice thermal storage system is often sized for the average load, not the peak load, it is smaller than the compressor for a traditional system. The smaller compressor horsepower means lower connected kW, which results in smaller transformers, switchgear, wire sizes and starter panels. If a facility uses a generator for daily or back-up power, the size of the generator will be significantly reduced when the peak electrical load of the facility is reduced using ice thermal storage. |
|
|
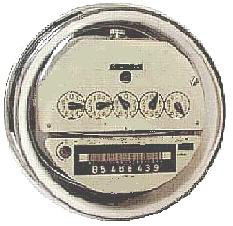 |
With less connected horsepower, ice storage can lower peak electrical demand for the process system by 50% or more. Since most electrical rates include demand times and/or higher day versus night kWh charges, savings on electrical bills can be substantial. Peak electrical demand rates of $15 to $18 per kW are not uncommon. In areas with “real time pricing”, where the electric rate varies hour-by-hour based on the market price of electricity, day-to-night kWh costs can vary by 500 to 1,000%. The use of electricity at night versus peak daytime hours can lead to large savings on energy bills. |
|
|
Although making ice requires more energy than producing chilled water, the efficiency penalty is not too large since the ice is made at night when condensing temperatures are lower. Because energy rates are lowest at night, the cost of building ice to produce cooling is less expensive than producing chilled water during the day. In addition, ice storage systems typically operate the chiller at full load which is very efficient. A process with a load that varies will have significant operating time with the chiller at reduced capacity and efficiency.
Ice thermal storage can reduce the process cooling time frame resulting in additional kWh savings. As the electric industry continues to deregulate, and time-of-use rates, real-time pricing schedules and negotiated power process become standard, ice storage can provide even greater future savings in operating costs. |

- Reduced Maintenance
|
The ice thermal storage coils have no moving parts so very little maintenance is required. The only ice thermal storage maintenance required includes the air blower (when required), system fluid and controls. Because the chillers and heat rejection equipment are smaller and there is less wear from compressor capacity adjustment, ice storage systems will have less maintenance than a traditional system. The ice thermal storage system also allows a chiller to undergo routine maintenance during the day when the ice storage can handle the system load. |
|